Optimising compressed air.
A compressed air generation and distribution system is a more or less complex assembly of machines, accessories and piping.
During the preliminary audit, a team of experts works together with the customer to carefully evaluate every aspect of the compressed air system, to provide an accurate assessment, identify areas for improvement and possible shortcomings, and to propose the best solutions from an operational and economic investment perspective.
Our technicians have devices to measure the electrical consumption of compressors and the flow rate they deliver. Thanks to Power System’s proprietary programs, we are able to analyse the performance of the existing system and simulate configurations with new machines and accessories, determining the potential for savings by adapting the compressed air system.
The expertise of our qualified technicians, combined with the energy performance of Power System compressors, allows users to minimise the effects of production activities on the environment.
The efficiency of a complex system such as a compressed air system passes through all its components. Our experts will guide you in choosing the most suitable treatment, storage and distribution accessories for your needs, always focusing on maximum energy efficiency.
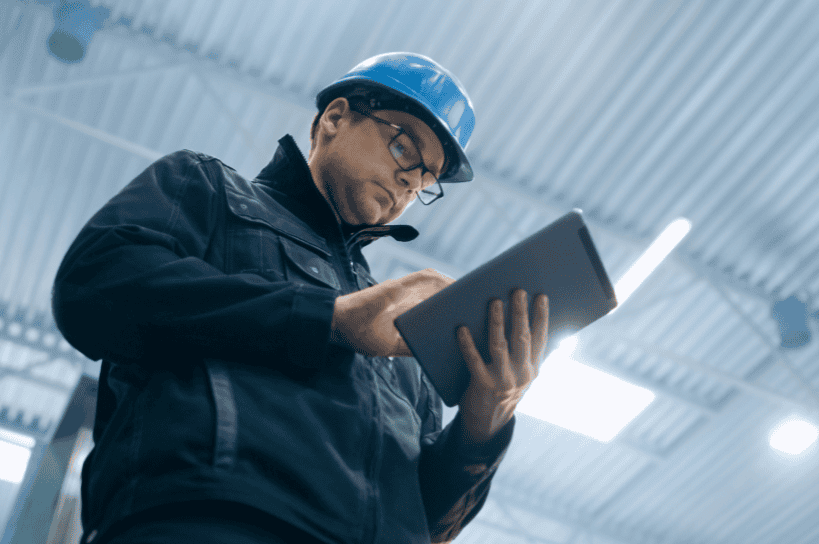
The service.
Depending on the complexity of the system and the type of analysis to be carried out, Power System Center technicians install various measuring devices for comprehensive monitoring: from the current drawn by individual compressors to the dew point obtained from the drying system.
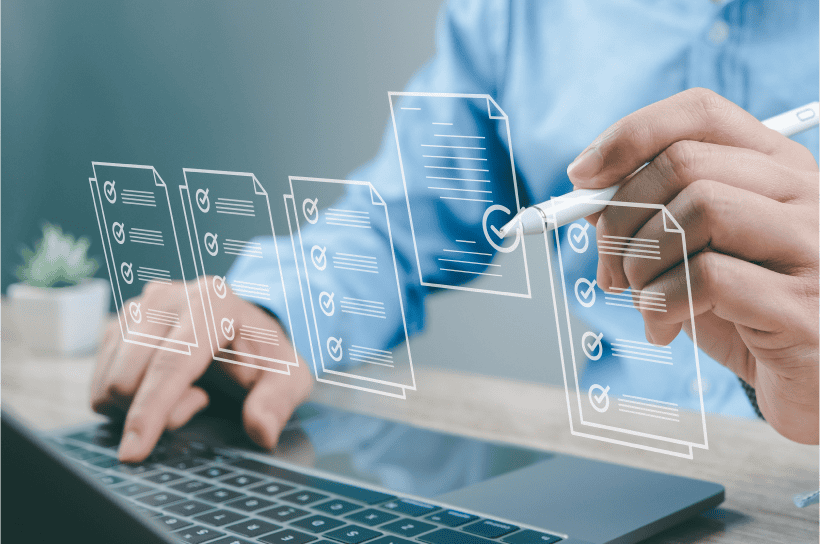
The final report.
The energy audit is declined in a report that includes a description of the state of the art, showing the values of the quantities monitored in the form of charts, and concluding with proposals for improvement and possible simulations for new components to be installed.
Mid-sized Italian company specialising in machining.
Upgrade and expansion of compressed air production station.
The existing system, based on a multi-machine solution, one of which was a single-stage variable speed machine, was causing control problems resulting in inadequate energy consumption.
Audit and complete redesign of the system by replacing the compressor described above with a double-stage variable speed NOBEL 2S 132 compressor.
20% reduction in energy consumption with an investment break-even point of less than 3 years.